以前溶接してから、久々に溶接を再開しました。
前回の溶接
前回ある程度満足できる結果が得られたので、この調子で行けるだろうと思ったら、失敗しました。
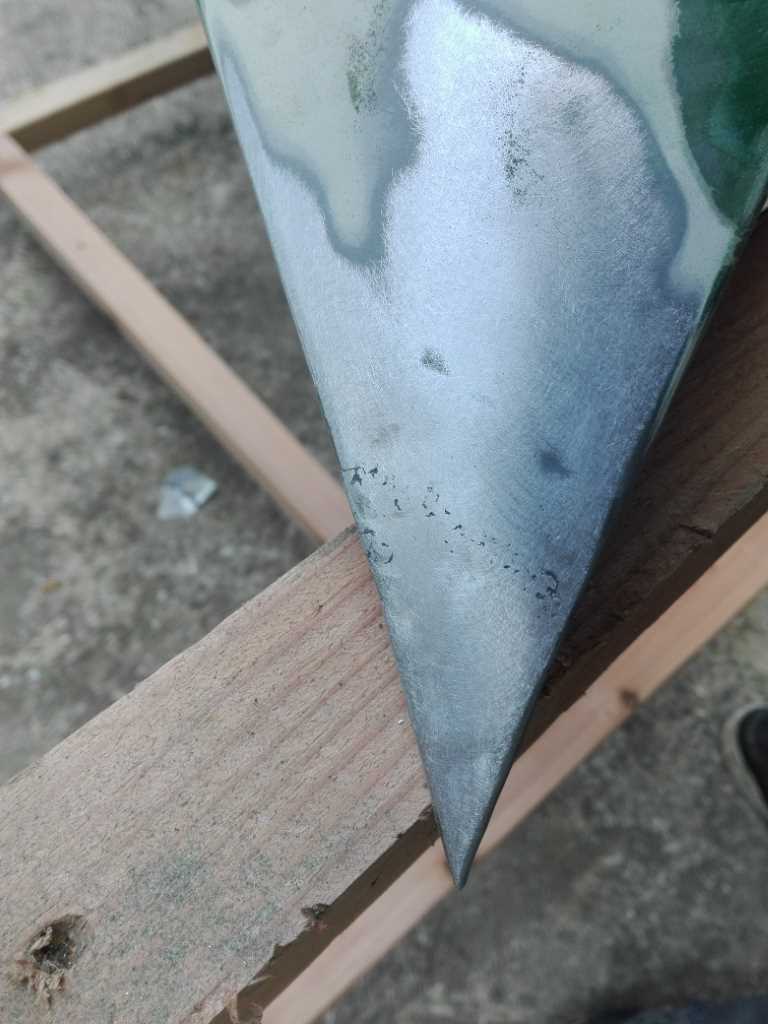
広がる溶接
それがこんな感じに、、、、最初は小さな穴を埋めるつもりだったんです、、。
でも穴をうめようとするとその脇に穴があき、さらにその穴を生めようとするとその脇に穴が、、、イタチごっこになって泥沼に、、。
形を整えてもう一回挑戦したい。
グッとスイッチを握ると、ジジッ!と音がしてアークが上がるのだけども溶け込み不良を気にして電流とダイヤルスピードは8目盛り中2にしていましたが、「ジジッ!」と音がした瞬間にたいていは穴が空いています。
0.8mm厚の鋼板ならまだよいが、0.6mm厚でさらにさびてるところなどはアルミホイルの如し。
ごくたまに溶けずにうまくいく場合の条件
- 接合面が隙間なく密着している。
- 表面に汚れが付着していない。
- 溶接ワイヤの先端をニッパーで切って行う。 ←面倒くさい。
→「ジッ!」でなんとかつながる。「ジ!」では溶け込み不良。「ジジッ!」で穴が空く
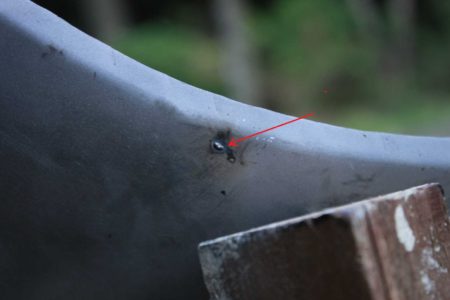
※「ジ」は個人差があります。あくまで感覚です。
逆にうまくいかない場合
- 接合面に0.5mm以上の隙間がある。
- さびて厚みが薄くなっている。
→穴が広がる。
- 表面が汚れている。
- ワイヤーの先端がダマ、またはススがついて汚れている。
→アークが飛ばず、溶け込みも少ない。
ネット上の動画などでは、溶け込んでいる動画などがあるが、ようやくそこで100vの限界を感じることになったわけです。
200Vだとどうなんだろう?といってもここに200V電源は無いし、、、と毎日ネットで調べたら、昇圧機というものがあることを知りました。
100Vから昇圧すれば、溶け込みがよくなるんだそうです。
昇圧機を購入
買ったのがこれ。25%アップができる、つまり125V電源で溶接機が使えるということです。
メーカーは溶接機に合わせてSUZUKIDを選択。
割と状態のよいところで溶接をしてみる。
一応裏側に鉄板をあてがって穴が空くのを軽減できないか、、、。
溶接したのがコレ。前より良い!まったく伝わらないと思うが、、、実はとてもうれしい。
点付けがそれぞれダマになっていて、一部にブローホールもあるが、溶け込みが段違い(個人比)に良い!
以前は球がのっているような感じだったのが、今はどら焼きみたいになってしっかり伸びているんです。
断面がなだらかに、場所によってはほど平になっているところもある。
そして、ダイヤルを1目盛り目にしてもちゃんしとアークが飛ぶ! ※失敗したアークは音が「バリ!」と言います。
感覚的な話ばかりですが、「ジ!」でダマ、「ジジ!」で平ら、「ジジッ!」でややふっくら、「ジジジ!」で穴が空く。
ともあれ、膨らみすぎた部分をベルトサンダーで平にし、点付けをつないでいきます。
大体のところでこんな感じ、、。削って面を整えるとね、隠れていた穴が見えてくるんです。
じゃ、ここから穴を埋めればよいのでは?と思いますが、しないほうが良い。なぜなら面を削って整えると板厚が薄くなるから。
爪でひっかる段差が概ね0.1mmあれば、その分薄くなっているかな、、、。多分0.5mmあればよいほうかと。
なので、これ以上は黒いスラグをサンドブラスターで取り除いて塗装してパテで埋めるのが良いと思い、ここであきらめることとした。
溶接の感想
角度を変えたり、トーチと鉄板の距離を変えることで、アークの出方が違うのがだんだんわかってきた。
穴埋めの方法もちょっとずつわかってきたかも、、点付けする度に、磨いて?ニッパーでワイヤーを切ってなんとか使えそうかな?
やっぱ200Vが良いのかな、、、。ぼちぼちですが、いろいろと試してみたい。
以上(2019/06/03記録)